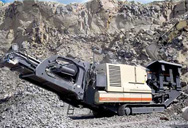
Ball milling: a green technology for the preparation and ...
The ball mill Ball milling is a mechanical technique widely used to grind powders into ne particles and blend materials.18 Being an environmentally-friendly, cost-effective technique, it has found wide application in industry all over the world. Since this mini-review mainly
Consulter un spécialiste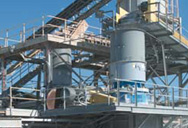
Process engineering with planetary ball mills
The present review focuses on the insight into several parameters like properties of grinding balls, the filling ratio or revolution speed. It gives
Consulter un spécialiste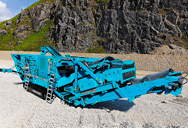
Grind - Molycop
SIZE Molycop manufactures forged grinding balls for use in ball milling and regrind applications in nominal sizes from 1.0” to 4.0” in diameter.
Consulter un spécialiste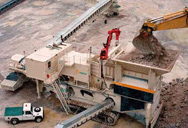
Grinding in Ball Mills: Modeling and Process Control
2012年6月1日 PDF The paper presents an overview of the current methodology and practice in modeling and control of the grinding
Consulter un spécialiste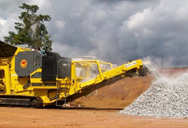
Ball Mill - an overview ScienceDirect Topics
Ball mills are commonly used for crushing and grinding the materials into an extremely fine form. The ball mill contains a hollow cylindrical shell that rotates about its axis. This cylinder is filled with balls that are made of stainless steel or rubber to the material contained in it.
Consulter un spécialiste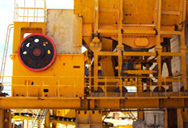
Process engineering with planetary ball mills
Processes inside planetary ball mills are complex and strongly depend on the processed material and synthesis and, thus, the optimum milling conditions have to be assessed for each individual system. The present
Consulter un spécialiste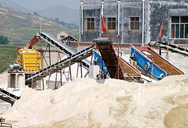
Ball milling: a green technology for the preparation
The ball mill allows applying mechanical forces in the presence of chemical agents, therefore it represents an ideal method to combine chemical and mechanical actions to obtain CNCs. Factors that should be taken into
Consulter un spécialiste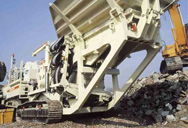
Grinding in Ball Mills: Modeling and Process
2012年6月1日 The paper presents an overview of the current methodology and practice in modeling and control of the grinding process in industrial ball mills. Basic kinetic and energy models of the grinding ...
Consulter un spécialiste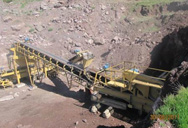
Ball Mill - an overview ScienceDirect Topics
Mechanical Crushing and Grinding. Oleg D. Neikov, in Handbook of Non-Ferrous Metal Powders, 2009 Tumbling Ball Mills. Tumbling ball mills or ball mills are most widely used in both wet and dry systems, in batch and continuous operations, and on a small and large scale.. Grinding elements in ball mills travel at different velocities. Therefore, collision
Consulter un spécialiste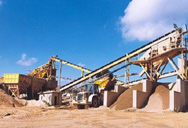
(PDF) Design of Three-chamber Ball Mill - ResearchGate
2021年1月1日 13m three chamber ball mill, ball grinding body is selected for the first and second chamber, ... Beijing: Chemical Industry Press, 2015.1:109-130. Effect of impeller size on SiO 2_ 2 Effect of ...
Consulter un spécialiste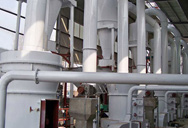
Optimal control of a ball mill grinding circuit—I. Grinding circuit ...
1991年1月1日 Chemical Engineering Science, Vol. 46, No, 3, pp. 551. 570, 1991. Printed in Great Britain, 0009 2509/hr $3.00 0.00 1991 Pergamon Press pic INTRODUCTION Ball mill grinding circuits constitute the primary unit
Consulter un spécialiste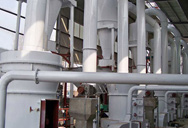
Design Method of Ball Mill by Sumitomo Chemical Co., Ltd.
Design Method of Ball Mill by Discrete Element Method collected. The diameter of the gibbsite powder was measured using a Master Sizer 2000 (Sysmex Corpora-tion). Details of the experimental conditions are given in Table 2. Results and Discussion 1. Effects of Fins on Ball Motion in the Mill To predict ball mill grinding behavior using the dis-
Consulter un spécialiste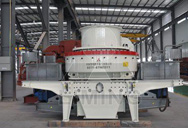
Speeding Up Your Organic Synthesis with Ball Mills
2015年4月7日 Application of Ball Mills in Organic Synthesis. The use of ball mills as reactors in organic synthesis is also driven by the concepts of process intensification and sustainable chemistry. Reaction conditions in
Consulter un spécialiste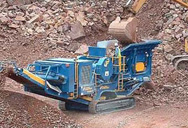
Ball Mill Grinding Characteristics with Respect to the Chemical ...
The ball mill grinding experiment employed a 20 (D) × 20 (H) cm mill and alumina balls at a volume filling of approximately 30% (J = 0.3), and each sample was injected 100% to the pore of the ball. The operation began with 69 rpm (70% of the critical speed) for 30 s, and the grinding time was doubled each time it was increased.
Consulter un spécialiste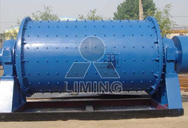
Dispersants in Stirred Ball Mill Grinding t - J-STAGE
grinding of dolomite in a stirred ball mill by using various chemicals to control the viscosity of the slurry being ground. 2. Experimental work 2-1 Mineral used Ground dolomite (size: 0-70 flm; specific gravity: 2.85 g/cm3) supplied by Ernstrom Mineral AB, Swe den, was used as the experimental material. Figure 1
Consulter un spécialiste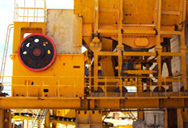
Process engineering with planetary ball mills
Processes inside planetary ball mills are complex and strongly depend on the processed material and synthesis and, thus, the optimum milling conditions have to be assessed for each individual system. The present
Consulter un spécialiste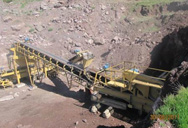
Ball Mill - an overview ScienceDirect Topics
Mechanical Crushing and Grinding. Oleg D. Neikov, in Handbook of Non-Ferrous Metal Powders, 2009 Tumbling Ball Mills. Tumbling ball mills or ball mills are most widely used in both wet and dry systems, in batch and continuous operations, and on a small and large scale.. Grinding elements in ball mills travel at different velocities. Therefore, collision
Consulter un spécialiste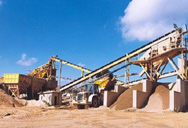
(PDF) Design of Three-chamber Ball Mill - ResearchGate
2021年1月1日 13m three chamber ball mill, ball grinding body is selected for the first and second chamber, ... Beijing: Chemical Industry Press, 2015.1:109-130. Effect of impeller size on SiO 2_ 2 Effect of ...
Consulter un spécialiste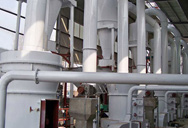
Optimal control of a ball mill grinding circuit—I. Grinding circuit ...
1991年1月1日 Chemical Engineering Science, Vol. 46, No, 3, pp. 551. 570, 1991. Printed in Great Britain, 0009 2509/hr $3.00 0.00 1991 Pergamon Press pic INTRODUCTION Ball mill grinding circuits constitute the primary unit
Consulter un spécialiste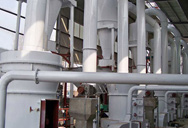
Design Method of Ball Mill by Sumitomo Chemical Co., Ltd.
Design Method of Ball Mill by Discrete Element Method collected. The diameter of the gibbsite powder was measured using a Master Sizer 2000 (Sysmex Corpora-tion). Details of the experimental conditions are given in Table 2. Results and Discussion 1. Effects of Fins on Ball Motion in the Mill To predict ball mill grinding behavior using the dis-
Consulter un spécialiste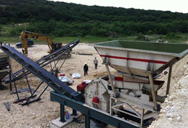
(PDF) Performance optimization of an industrial ball
2017年1月1日 Abstract. In this investigation, we optimize the grinding circuit of a typical chromite beneficiation plant in India. The run-of-mine ore is reduced to a particle size of less than 1 mm in the ...
Consulter un spécialiste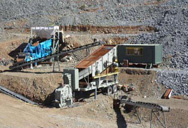
Ball Mill Grinding Theory - Crushing Motion/Action
2017年4月28日 It seems certain, however, that the ball-mill will crush to 200 mesh a considerably greater tonnage when the proper classification is provided. Since in previous tests the mill has crushed 7½ T. per hr. from
Consulter un spécialiste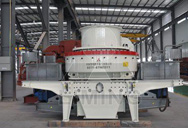
Speeding Up Your Organic Synthesis with Ball Mills
2015年4月7日 Application of Ball Mills in Organic Synthesis. The use of ball mills as reactors in organic synthesis is also driven by the concepts of process intensification and sustainable chemistry. Reaction conditions in
Consulter un spécialiste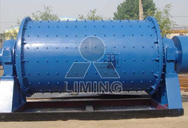
Dispersants in Stirred Ball Mill Grinding t - J-STAGE
grinding of dolomite in a stirred ball mill by using various chemicals to control the viscosity of the slurry being ground. 2. Experimental work 2-1 Mineral used Ground dolomite (size: 0-70 flm; specific gravity: 2.85 g/cm3) supplied by Ernstrom Mineral AB, Swe den, was used as the experimental material. Figure 1
Consulter un spécialiste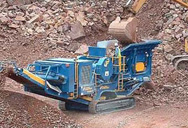
Ball Mill Grinding Characteristics with Respect to the Chemical ...
The ball mill grinding experiment employed a 20 (D) × 20 (H) cm mill and alumina balls at a volume filling of approximately 30% (J = 0.3), and each sample was injected 100% to the pore of the ball. The operation began with 69 rpm (70% of the critical speed) for 30 s, and the grinding time was doubled each time it was increased.
Consulter un spécialiste